Read the Rotex whitepaper on how various types of bulk material screening motions can impact performance here.
All types of bulk material screening require a screener that uses screen motion to create an acceleration between the screen and material. The two most commonly used motions are described below.
Vibratory
For many engineers, their first thought on how to screen material is to use a vibratory screener. It seems like simple common sense that this will be the most efficient. Two styles of vibratory screeners exist. They are rectangular units whose motions imitate a vibrating conveyor or feeder and a round screener. Both are reasonable choices for applications where the screening application is easy like getting marbles out of sand.
The Achille’s heel of vibratory screeners is that lack of capacity or accurate screening. The issue is that vibration works by tossing material into the air and hoping it lands so that smaller particles pass through the screen. A vibrating screen is obviously a moving target and this process of using random chance to screen has proven inefficient. Either a larger hole must be used (thus reducing accuracy) or a lower process rate must be specified.
Gyratory Reciprocating
By contrast, very few (if any) engineers ever start their search for a screener by thinking that a modified gyratory reciprocating motion is the preferred method. Heck, most don’t even know what that means.
This screening motion uses a crank pin at the inlet end to create a circular motion. Material lands on the screen and immediately spreads out across its width by rolling over the screen openings. The small particles begin dropping through the screen immediately.
As material travels down the screen, the gyratory motion segregates the material flow with the smaller particles working their way down to the bottom and through the screen. The larger particles begin riding on the top of the material flow and will pass over the end of the screen.
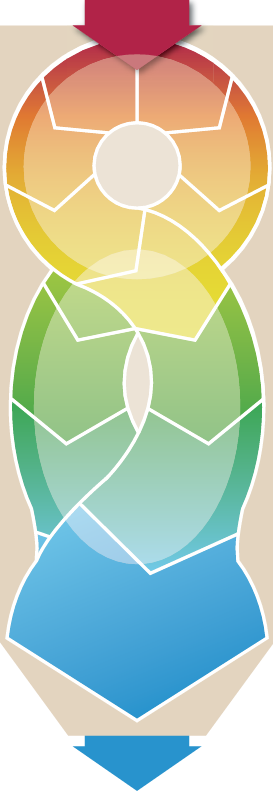
At the discharge end of the screener the motion is constrained to reciprocate forward to back. This motion pumps the remaining larger particles off of the screen to maintain a clear screen that can process large flows of material.
It all boils down to a consideration of accuracy vs efficiency.
For more assistance in choosing the right machinery for your materials processing, Mills-Winfield is here to help. Our representatives can discuss all aspects of your projects to help you determine the equipment you need.